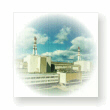
Brief
Description of Ignalina Nuclear Power Plant:
The Ignalina
nuclear power plant contains RBMK-1500 water-cooled graphite-moderated channel-type
power reactors.
The RBMK-1500reactor is the largest power reactor in the world.
The thermal power output of one unit is 4800 MW, the electrical
power capacity is 1500 MW.
The Ignalina nuclear power plant, like all stations with RBMK
reactors, has a direct cycle configuration - saturated steam
formed in the reactor proper by passing the light water through
the reactor core is fed to the turbine at a pressure of 6,5 MPa.
The light water circulates over a closed circuit.
The first stage of the nuclear power project comprises two units.
The unit with one reactor contains two 750 MW turbines.
Eeach generating unit is provided with a fuel handling system and
unit control room.
The turbine room, waste gas purification and water conditioning
rooms are common for all the units.
- "Reactor design"
- "Technical data on RBMK-1500
reactor"
- "Circulating circuit"
- "Steam and condensate feed
circuit"
- "Turbogenerator sets"
- "Fuel loading system"
- "Station control and monitoring
system"
- "Reactor control and protection
system"
- "Reactor process monitoring
system"
- "Radiation safety"
1.
Reactor design:
The main structural element of the reactor, a graphite stack with
fuel channels, absorber-rods and surrounding metal structures, is
housed in a concrete vault.
The vertical graphite stack columns contain fuel channels and
control rod channels.
The graphite stack is carried by a welded steel structure resting
on a concrete foundation.
On top the graphite stack is spanned over by an upper steel
structure resting on the annular water tank of the biological
shield.
A welded shell enclosing the graphite stack, as well as the upper
and bottom steel structures form a sealed reactor space.
To prevent graphite oxidation and to improve heat transfer from
graphite to fuel channels, the reactor space is filled with a
helium-nitrogen mixture.
Provision is made to replace the fuel channels and control rod
channels on the shut-down and cooled reactor.
The fuel channels are tubes whose lower and upper portions are
fabricated from corrosion-resistant steel, while the central part
is made of Zircalloy.
The split graphite rings in the channels provide thermal contact
with the graphite bricks of the stack.
Suspended in the fuel channel is a fuel assembly bank.
The fuel assembly bank consists of two fuel assebmlies.
Each fuel assembly contains 18 fuel rods in the form of sealed
Zircalloy tubes which are filled with uranium dioxide pellets.
Light water coolant is fed into the lower end of the fuel
channels.
From the fuel channel the coolant in the form of steam/water
mixture goes into the separators.
To improve heat exchange, the upper fuel assembly carries special
intensifying grids.
Removal of irradiated fuel elements, their handling and charge of
fresh elements are performed on load by means of a refuelling
machine mounted in the central room.
The biological shield is made of carbon steel, serpentine crushed
stone and gravel, concrete, sand, water.
2.
Technical data on RBMK-1500 reactor:
Coolant
light water (steam/water mixture)
Heat cycle configurationsingle-circuit
Reactor power, MW:
Core
dimensions, mm:
Square
lattice pitch, m 0.25x0.25
Thickness of graphite reflector, mm:
Maximum
graphite temperature, C' 750
Fuel
Initial
enrichment, for 235U, % 2.0
Rate of fuel burnup, MW d/kg 21.6
Number of channels per lattice, pc:
Saturated
steam pressure in separators, MPa 7.0
Feed water temperature, C'190
Saturated steam flow rate, t/h 8800
Coolant flow rate through reactor, m3/h 40000 : 48000
Coolant temperature, C':
Mean
mass steam content at outlet 0.291
3.
Circulating circuit:
The
circulating circuit of the reactor is a system composed of fuel
channels, steam/water and water lines, steam separators, main
circulation pumps, pressure, suction and distribution headers
with associated piping.
The circulating circuit consists of two loops.
Each loop contains two horizontal type steam separators
interconnected on the water and steam sides.
Each separator houses inside a feedwater header.
Feedwater flows from the header into downcomers through
perforated nozzles.
The separated water, in mixing with the conditioned, heated, and
deaerated feedwater goes through the downcomers to the suction
header and then is conveyed via suction pipes to the four main
circulating pumps one of which is kept in the stand-by duty.
The pumps are of a vertical, centrifugal, single-stage
configuration.
The rated pump delivery is 8500 cu.m/h at a head of 200 m w.g.,
speed - 1000 rpm, electric motor output - 5500 kW.
The delivery pipelines convey water from the main circulating
pumps to the pressure header.
The suction line of each main circulating pump is provided with a
stop gate, the delivery line (down the flow) mounts a check
valve, a throttle valve and a stop gate.
The suction and pressure headers of each loop are interconnected
by six bypass lines, each provided with a stop gate and a check
valve.
The bypass lines maintain natural circulation of coolant at
emergency shutdown of a main circulating pump.
The pressure header is connected through pipes with 20
distribution headers.
On the upstream end, each distribution header is provided with a
stop gate, a check valve and a mixer for water coming from the
reactor emergency cooling system. 40-43 water supply lines are
branched off each distribution header.
Each loop effects heat removal from half the reactor.
The coolant flow distribution among the fuel channels as a
function of the core energy release is controlled by shutoff
control valves following the indications of flow meters mounted
at the inlet of water supply line to each fuel channel.
4.
Steam and condensate feed circuit:
Steam is conveyed from each separator to the turbines over two
steam lines.
The steam piping is so arranged that each steam separator is
connected with two turbines.
The equipment and pipelines are protected against excessive
pressure rise by a system of steam dumping facilities which dump
excess steam into the turbine condensers or into the condensation
pools of the accident isolation system.
The condensate of the steam spent in the turbines is conditioned
in the ion-exchangers, heated in the heat exchangers of the
regenerative heating system, deaerated and on passing through
strainers is fed back by the electric feedwater pumps over feed
pipelines to the separators of the circulating circuit.
5.
Turbogenerator sets:
Each unit contains two K-750-65/3000 turbines with 800 MW
generators.
The turbines are double-flow tandem machines (one high-pressure
cylinder and four low-pressure cylinders) with reheat.
The rotor speed is 3000 rpm.
The three-phase 50 Hz generators with hydrogen and water cooling
are connected to the outdoor substation.
The turbines are controlled by cumputer-based control system
ASUT-750.
6.
Fuel loading system:
Fuel is charged and discharged by means of a refuelling machine
while the reactor is on load.
The main element of the refuelling machine is a casque with a
biological shield designed to take the working pressure within
the fuel channels and equipped with mechanisms serving the following
functions:
- canning of the machine with the upper portion of the fuel
channel;
- depressurization and pressurization of the fuel channel cap;
- removal of spent fuel assembly bank with suspension;
- inspection of the fuel channel tract;
- loading of fresh fuel assembly banks.
The refuelling machine is provided with two systems of precise
positioning over the fuel channel-optical/television and contact.
The casque is mounted on a bogie moving along a bridge rail-bound
in the central room.
The refuelling machine is controlled from the operator`s room
which is located behind the wall of the central room.
7.
Station control and monitoring systems:
The control and monitoring systems provide reliable and safe
operation of the major equipment and maintain stable process
parameters.
Functionally the monitoring and control systems comprise:
- reactor control and protection system;
- control and protection system of reactor process equipment;
- control and protection system of turbogenerator and outdoor
switchgear;
- functional group control system;
- refuelling machine control system.
Most of process parameters are monitored by a data logging
system.
Control data are displayed on the unit control board using VDU,
visual and recording instuments, various announciation windows
and indicators, mimic diagrams and printers.
The station is controlled from the unit control board.
General control and coordination of the operators work are
responsibilities of the shift chief or his deputy.
The station incorporates provision for multiple protection of
proccess equipment.
Malfunction of the process equipment initiates operation of
various kinds of protective gear providing controlled reduction
of the reactor power at a rate of 2-4 per cent/s to the safe level.
The reactivity scramming which brings the reactor power down to
zero, is applied in rare cases.
8.
Reactor control and protection system:
The control and protection system is intended for reliable
follow-up of the reactor performance and its safe operation.
The system provides start-up, automatic maintenance of power at
the set level, allows control of energy distribution along the
radius and heightwise of the core, compensates for fuel burn-up,
provides protection of the reactor under emergency conditions.
The control and protection system is built of fail-safe and
redundant devices using integrated curcuits to receive and
process signals from various sensors, as well as to present the reactor status
information to the operator.
The reactor power release and its distribution are controlled by
211 carbide boron rods placed in the control channels and moved
by individual servomotors mounted on the top of the control cannels.
The control rods are cooled with water from a special loop.
Out of the total number of rods, 40 ones are used for energy
distribution control through the hight of the active zone of the
reactor.
24 rods perform the function of prompt emergency safequard
introduced into the active zone within 2.5 seconds under definite
emergensy situations.
The remaining rods are unified and serve the function of
reactivity scramming, automatic maintenance of the reactor power
release at the set level, control of energy distribution over the
core radius.
9.
Reactor process monitoring system:
The reactor process monitoring system provides the operating
personnel with information and inputs data into the control and
protection system.
The reactor process monitoring system consists of the following
functional elements:
- data logging system which provides follow-up, processing and
presentation of the data;
- self-contained energy release control system which provides
measurement, control and indication of energy release in the
reactor channels;
- self-contained system monitoring tightness of fuel assembly
cladding and providing measurement, control and indication of
coolant activity rise;
- system monitoring integrity of the fuel and control channels
and providing measurement of temperature and indication of
relative humidity of gas pumped through the gas paths of the
core;
- system monitoring coolant flow in the reactor channels;
- system monitoring temperature of the main and auxiliary
equipment of the reactor.
The data logging system is configured in a three-level hierarchy
using computers SM-1M and SM-2M and interface facilities.
The energy release monitoring and control system includes energy
release detectors providing inertialess measurement of neutron
flux density along the radius and height of the core, and the equipment
to process information and signals on the contol board.
The system monitoring tightness of the fuel assembly claddings
includes scintillation gamma-spectrometer sensors, equipment, to
ensure operation and movement of sensors in the intertube space
of the steam lines, and facilities for processing and output of
data.
The system monitoring the coolant flow through the reactor
channels consists of tachometric transducers, and equipment
affording frequency-to-analog signal conversion.
The system monitoring the temperature of the reactor equipment
contains mainly heat-resistant cable heat-electric transducers.
10. Radiation safety:
The RBMK-1500 reactor is provided with special elements and
systems ensuring radiation safety of the nuclear power plant and
the environment both under normal operating conditions and in the
emergency cases.
The radiation safety and doze control systems include:
- highly reliable computerized control and protection system;
- reactor scram system;
- accident isolation system;
- fuel rod cladding tightness monitoring system;
- special facilities for gaseous effluent purification;
- liquid radiowaste discharge, processing and hold-up system;
- computerized radiation doze control system;
- computerized system monitoring gaseous emissions and liquid
waste discharges;
- facilities for environmental radiation dose control.
The system monitoring tightness of fuel rod cladding specially
designed for the RBMK-1500 reactors and applying modern
techniques for detection of faulty fuel rods and computer-based data
logging provides the core radiation control.
The computerized radiation doze control system at the nuclear
power plants with reactors of the RBMK-1500 type is provided with
facilities monitoring radiation exposure of all components and
systems of the station.
All this helps to maintain the radiation conditions at a safe
level by implementing the purposeful actions (removal of leaky
fuel assemblies, decontamination, replacement and repair of the equipment).
To reduce emissions of noble radioactive gases.
A two-stage system is used for cleaning gaseous and aerosol
effluents discharged through a 150 m high stack into the
atmosphere.
The first stage includes a hold-up chamber.
When noble gases pass through it, their activity is reduced due
to natural decay.
The second stage-activity suppression facility purifies and
reduces activity of noble radioactive gases by the method of
dynamic sorption using the radiochromatographic char columns.
To reduce radioactive aerosol emissions at the nuclear power
plants with the RBMK-1500 reactors provision is made for
purification facilities absorbing aerosols by special filters.
The nuclear power plants with the RBMK-1500 reactors use a
closed-circuit water supply system.
Liquid radioactive effluents undergo special treatment.
Radioactive discharge into air and water is monitored
continuously using instruments of the computerized radiation dose
control system.
The external radiation exposure surveillance service at the
nuclear power plant with the RBMK-1500 is equipped with
instruments to analyze concentration of radionuclides in the elements
of the environment.
The health physics laboratory is provided with facilities and
sampling methods, dozimetric, radiometric, spectrometric
instruments for objective assessment of the radiation conditions in the
environment.
GO
TO WWW.IAE.LT HOME PAGE
GO TO INPP PAGE
If You have any
comments or suggestions on our page, please E-mail them to the
page maintainer .
This page is maintained by Michael Laenko (michael@iae.lt ).
Copyright
©1996 Ignalina NPP. All right reserved.
Joseph Gonyeau. Copyright
© 1996 Cannon Valley Web-Lynx.
All rights reserved. Revised: September 14, 1996